Soldering Heat Sink
Different materials can be welded together through surface nickel plating at low temperatures and without the need for vacuum, such as aluminum fins and copper base plates of heat sink, and vice versa. This is a low-cost and efficient production process for making heae sink.
What Is A Soldering Heat Sink?
The soldering process of heat sink is also a common process, which is widely used in the field of cooling solutions production technology. In the soldring heat sink with heat pipes ,due to the need for higher density heat dissipation area, the fin must be very small, generally 0.1 to 0.4mm thickness. Profile process or shkived fin process is difficult to achieve such a small thickness.
Generally speaking, the use of stamping tooling can be in accordance with the design of continuous fin pieces, usually made of aluminum, but need to be welded with aluminum base, it must be coated with a layer of nickel, and then solder them up with tin paste after high temperature. Similarly, if the material is copper, the two material can be welded together at 140- 180 degrees without the need for nickel plating.
The soldering heat pipes heat sink with good heat dissipation performance, which provides reliable heat dissipation performance guarantee for electronic components. Soldering welded heat sink can usually meet high density heat dissipation requirements, because the heat accumulation of the chip is more concentrated.
What Are The Characteristics of The Soldering Heat Sinks?
● The material is generally Al 1100,6061,6063,C1100;
● The surface of the material needs to be nickel plated before welding
● The heat sink surface can be sprayed with oil or powder;
● Heat sink product needs tooling for making stamping fins
● Product processing time is relatively low, high production efficiency
● Our usual process of making this product is to get the customer’s drawing, we will do the DFM feedback, and then make the sample. After the sample is finally confirmed, we will mass produce;
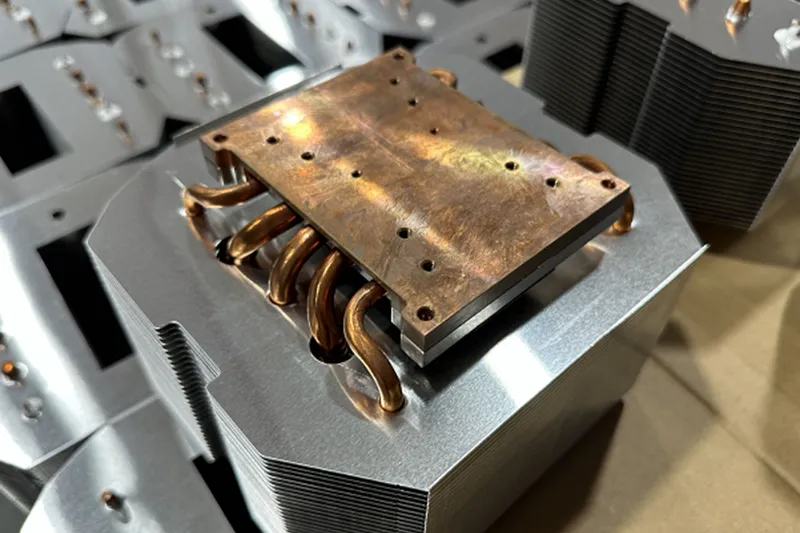
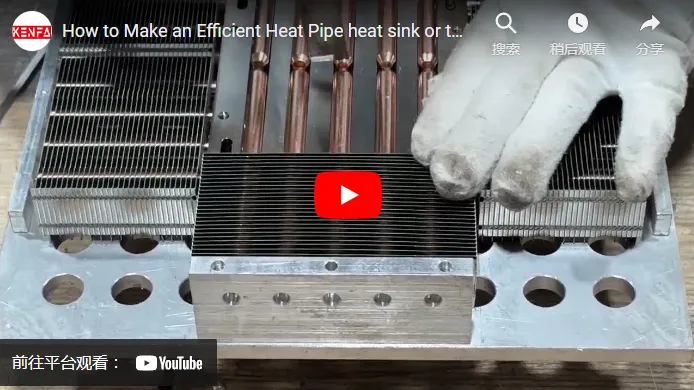
How To Make A Soldering Heat Sink?
Materials need to be prepared, usually copper and aluminum materials are welded together. This requires a surface layer of nickel plating, mainly because the chemical properties determine that the solder paste can be welded together under high temperature conditions. Of course, there are also copper materials or aluminum materials welded together.
After preparing the materials, it is necessary to clean the surface and remove the surface moisture of copper or aluminum. At this time, we usually brush the solder paste on the bottom plate of the radiator once, then place the fin on it, fix it directly, and under the action of mechanical force, evenly press these two components.
As mentioned earlier, sometimes it is necessary to solve the problem of high-density heat dissipation. At this time, suitable heat pipes can be added to utilize the super thermal conductivity of the heat pipes to solve the heat transfer problem. At this time, the heat pipes can be fixed in a suitable position, and the base plate, fin plate, and heat pipe can be fixed together. They are placed in a high-temperature reflow furnace at 180-230 degrees Celsius, and the solder paste will quickly melt and connect to the three components. After cooling, The three components connected will be very sturdy, and it is best to clean them again to make an efficient heat sink.
When Will The Soldering Process Be Used To Make A Heat Sink?
● High density heat dissipation performance is required, and the product size is very high, and the fin sheet is relatively thin, with a thickness of less than 0.5mm
● The selected material is a combination of copper and aluminum solution
●The heat is relatively concentrated or needs to be transferred to another place, and there is also a need to transfer the heat to the fin in an instant.
● When we need a large-scale production and modular structural product, it has high production efficiency and low cost, such as laptop cooling modules, etc.
● When your structural space is limited and other profile processes and shovel fin processes cannot meet the requirements.
● Soldering paste welding is a reliable and flexible process. When designing, it is necessary to consider the mold cost of the fin. Moreover, the welded product usually needs to be used indoors, and if used outdoors, it needs to be painted or sprayed, which is a very important .
How to Control the Quality of Our Products?
we prioritize quality above all. Our comprehensive quality control measures ensure the reliability and durability of our products. Each liquid cold plate undergoes rigorous testing for thermal performance, structural integrity, and fluid tightness to meet our high standards. Our team of experts scrutinizes every stage of the design, development, and production process, ensuring each product that leaves our facility stands as a testament to our commitment to excellence.
We recognize that product quality issues and delivery delays are prevalent pain points in our industry. Therefore, we’ve implemented strict production management protocols and a robust supply chain strategy to mitigate these issues. By synchronizing our production schedules with our clients’ timelines, we ensure timely delivery of products without compromising on quality. Choose Kenfatech, where we merge impeccable quality with punctual delivery, providing you with seamless service and peace of mind.
At the same time, we also value customer feedback, such as problems found during use and installation of products, which can be fed back to our business and after-sales personnel. Our regular quality meetings on Wednesdays will focus on discussing these problems to prevent and prevent future occurrences. Of course, in terms of process improvement and process stability, we often improve, The purpose of updating and upgrading software for machine equipment is to ensure the reliability and stability of our products, without any quality issues occurring

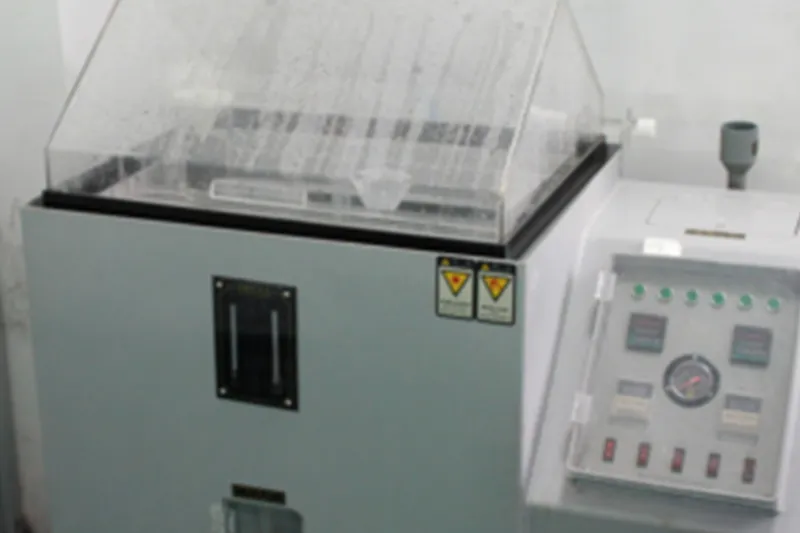
Standard Specification Dimensions Are as Follows:
You can click on the part number below to view the detailed page, and our drawings are available for download.
(Length X Width X High,Unit mm)
Part Number | Size(mm) | Material | Drawing |
KF-HS1008953-150W | 101X89X53mm | Aluminum ,Heat pipes,Fans | Detail information |
KF-HS1239051-200W | 123x90x51mm | Aluminum ,Heat pipes,Fans | Detail information |
KF-HS1288953-250W | 128X89X53mm | Aluminum ,Heat pipes,Fans | Detail information |
KF-HS1289098-300W | 128X90X98mm | Aluminum ,Heat pipes,Fans | Detail information |
KF-HS1329096-350WA | 132X90X96mm | Aluminum ,Heat pipes,Fans | Detail information |
KF-HS9086112-350WC | 90X86X112mm | Aluminum ,Heat pipes,Fans | Detail information |
KF-HS14212467-400WA | 142X124X67mm | Aluminum ,Heat pipes,Fans | Detail information |
KF-HS14212467-400WB | 148X124X86mm | Aluminum ,Heat pipes,Fans | Detail information |
KF-HS22412467-500WA | 224X124X67mm | Aluminum ,Heat pipes,Fans | Detail information |
KF-HS20712486-600W | 207124X86mm | Aluminum ,Heat pipes,Fans | Detail information |
KF-HS236120103-800WA | 236X120X103mm | Aluminum ,Heat pipes,Fans | Detail information |
KF-HS29012486-800WB | 290X124X86mm | Aluminum ,Heat pipes,Fans | Detail information |
KF-HS28925044-1000WA | 289X250X44mm | Aluminum ,Heat pipes,Fans | Detail information |
KF-HS240120103-1000WB | 240X120X103mm | Aluminum ,Heat pipes,Fans | Detail information |
KF-HS240120103-1000WC | 288X124X127mm | Aluminum ,Heat pipes,Fans | Detail information |
KF-HS28928046-1200W | 289X280X46mm | Aluminum ,Heat pipes,Fans | Detail information |
KF-HS292130166-1400W | 292X130X166mm | Aluminum ,Heat pipes,Fans | Detail information |
Since this kind of products are customized, but we have relative standard products,If you need to customize or know detailed products, you can contact us.
The standard parts:
150W 101x89x53