IGBT Cooling Applications
IGBT module is composed of IGBT and FWD(diode chip) through a specific circuit bridge packaging modular semiconductor products; The packaged IGBT module is directly used in frequency converter, UPS uninterrupted power supply and other equipment.
IGBT Thermal Management.
The thermal management of IGBT (Insulated Gate Bipolar Transistor) is of critical significance in the field of power electronics. As the heat generated by the current passing through the device increases, an effective heat dissipation system becomes a key factor in ensuring device performance and lifespan. For this reason, well-designed heat sink is essential to effectively transfer heat to the external environment. Thermal interface materials such as heat pipes and heat dissipation adhesives help improve thermal conductivity efficiency and ensure uniform surface temperature of the device.
The temperature monitoring and control system monitors the temperature of components in real time by installing temperature sensors at critical locations and taking measures to prevent overheating. This includes automatically adjusting the current or reducing the operating frequency to ensure that the device operates within the rated temperature range. Taking into account the design of heat sinks, liquid cold plate ,thermal interface materials, and intelligent temperature control, the reliability and performance of the system can be effectively improved, ensuring the stable operation of IGBTs in high-pressure and high-temperature environments.
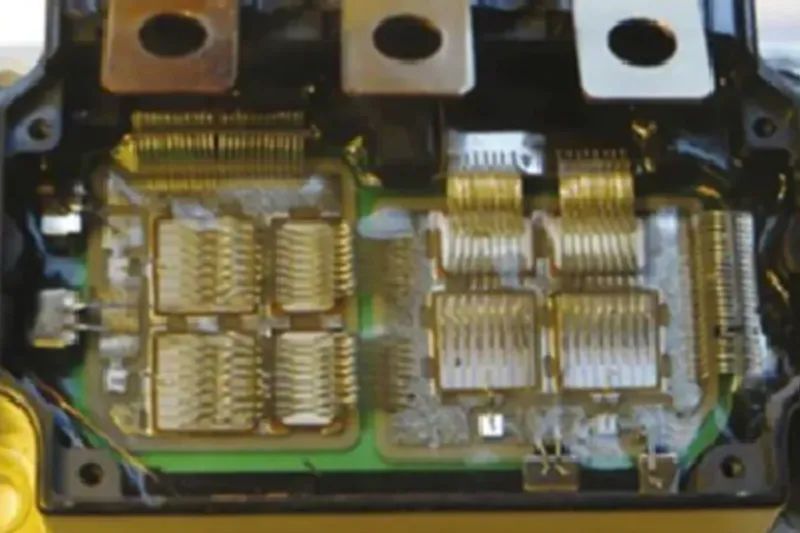
How To Design IGBT Heat Sinks.
The design of IGBT heat sink is a crucial part. Adopting advanced three-dimensional structures, such as optimizing the shape of fins, to maximize the contact area with air and improve thermal conductivity efficiency. At the same time, high thermal conductivity materials such as copper or aluminum are used to ensure rapid conduction of thermal energy to the surface. The design of air duct structure plays a crucial role in the performance of air-cooled heat sinks.
By designing a reasonable guide vane and air duct, optimization of fluid dynamics is achieved, guiding air through heat sensitive areas and maximizing cooling effectiveness. A meticulous air duct design can reduce the resistance of air flow and improve heat dissipation efficiency. Fan control technology is also an essential aspect that cannot be ignored. Adopting an intelligent fan control system, adjust the fan speed based on real-time temperature monitoring data. At low loads, the fan speed can be reduced to reduce noise and energy consumption, while at high loads, increasing the speed can enhance cooling effectiveness.the system can be effectively improved, ensuring the stable operation of IGBTs in high-pressure and high-temperature environments.
How To Design IGBT Liquid Cooling Plate.
The design of liquid cooled plate heat dissipation is to efficiently reduce the temperature of IGBT and ensure the stability of the device during high-power operation. Its material selection is crucial. Using high thermal conductivity metal materials, such as copper or aluminum, to ensure good thermal conductivity. These materials can effectively transfer the heat generated by the device quickly to the surface of the liquid cooled plate. The flow channel of the liquid cooling plate is also very important, which is an important place for heat exchange.
Usually, high-density shovel fins are arranged under the installation of IGBT, which is conducive to efficient heat exchange between skived fin and coolant. The design of liquid cooling systems also needs to consider the issues of fluid circulation and flow velocity. By designing the liquid cooling pipeline and flow direction reasonably, it is ensured that the coolant can fully cover the entire surface of the liquid cooling plate and quickly remove heat.Intelligent control system is another important aspect of liquid cooling plate design. By installing temperature sensors at critical locations, the temperature of the IGBT is monitored in real-time, and the flow rate and temperature of the coolant are adjusted as needed to ensure that the device operates within a safe temperature environments.
Simulation Analysis of IGBT Core Temperature.
Quality control is crucial when producing 5G communication heat sinks. Firstly, ensure that the quality of raw materials meets the standards and use materials with high thermal conductivity, such as high-quality metals and heat dissipation adhesives. Secondly, establish a precise production process, implement strict manufacturing standards, and ensure that the manufacturing process of each heat sink complies with design specifications.
Adopting automated equipment and advanced production technology to improve production efficiency while reducing human error. During the production process, regular quality inspections and sampling inspections are carried out to ensure that the products meet the design requirements. Finally, establish a comprehensive after-sales service and traceability system to track and improve potential issues, in order to ensure the long-term stability of the product and customer satisfaction. Through these control measures, it can be ensured that the 5G communication heat sink maintains high quality during the production process and meets market demand.
How to Design Flow Channes For A IGBT Liquid Cold Plate?
The liquid cold plate is typically made of a flat metal material with a series of internal channels. The design of the channels should ensure uniform flow of the cooling medium (typically water) to effectively cool the entire surface of the IGBT. Common channel structures include straight, helical, and parallel designs.The dimensions of the channels should be determined based on the power density and thermal characteristics of the IGBT device. The width, depth, and spacing of the channels should allow the cooling medium to adequately cover the surface of the IGBT and provide sufficient flow space for effective cooling.
The channel layout should consider the thermal distribution of the IGBT device. Typically, the channels should be concentrated in the hot spot region of the IGBT, where the heat is highest, to maximize temperature reduction.The channels of the water-cooling plate need to be connected to an external cooling system (such as a water cooling system). The connection can be designed as a straight-through arrangement for the inlet and outlet, or it can involve threaded interfaces or pipe connections.
To enhance cooling effectiveness, flow control devices such as helical fins or flow diverters can be incorporated within the channels. These devices help increase heat exchange between the cooling medium and the IGBT, thereby improving cooling efficiency.The channels are typically made of metal materials with good thermal conductivity, such as copper or aluminum. Choosing suitable materials can enhance heat transfer efficiency, ensuring rapid absorption and dissipation of heat by the cooling medium.
During the actual design process, the flow channel structure and parameters of the IGBT water-cooling plate need to be optimized and adjusted according to specific application requirements, IGBT device specifications, and operating conditions. Therefore, it is recommended to collaborate with professional engineers or domain experts to ensure that the water-cooling plate design meets system requirements and provides effective cooling performance.
Controlling The Machining Dimensions of IGBT Heat Sinks .
It is a crucial step in ensuring their performance and stability. Strict production standards and regulations need to be established to clarify the design requirements for heat sinks. By implementing reasonable dimensional tolerances and quality control standards, ensure that each processing step complies with the specified dimensional range. Meanwhile, high-precision processing equipment and process flow are adopted. CNC machine tools and advanced production processes can ensure the accuracy and stability of processing.
Regularly maintain and calibrate production equipment to ensure stable performance and reduce dimensional deviations caused by equipment errors. Implement strict quality inspection processes. By using high-precision measuring equipment such as coordinate measuring machines, a comprehensive dimensional inspection of the heat sink is carried out to ensure that the product meets the design specifications. Qualified products enter the next step of the process, while products with dimensional deviations need to be adjusted or eliminated in a timely manner. Finally, establish a feedback mechanism to continuously monitor and analyze production data, promptly identify issues in size control, and take corrective measures. This helps to continuously optimize the machining process, improve the consistency and stability of the heat sink machining dimensions.
Why choose Kenfa's IGBT heat sinks.
Our advantage in designing and manufacturing IGBT heat sink lies in our comprehensive engineering capabilities and technical strength. Firstly, we have an experienced engineering team with deep knowledge in the fields of power electronics and thermal management, capable of providing customized design solutions according to customer needs. Secondly, we have introduced advanced simulation techniques to accurately analyze the thermal characteristics of IGBT through numerical and thermal simulations, providing scientific basis for heat sink design. In addition, we use high-precision processing equipment and automated production lines to ensure the manufacturing accuracy and consistency of the heat sink. Our products also focus on the selection of production processes, such as the shovel fin radiator, which can meet the current heat dissipation needs of all high-power IGBTs, to ensure maximum heat dissipation effect and cost advantage.t
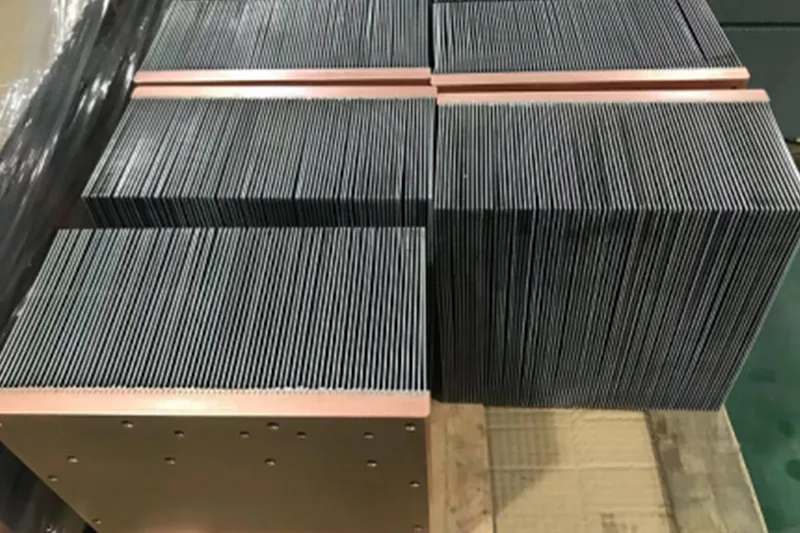
Blogs and academic papers on cooling solutions for IGBT
What is IGBT heat dissipation? What kind of liquid cooling plate design is optimal, and how the cold plate microchannel of IGBT is designed. These theoretical data and research have been accumulated and organized by us. Through the experience of engineers and the understanding of the design process, we have written some blog articles. The content of these articles can clearly reflect our research on high-power IGBT radiators, and our understanding of the process is very experienced, which can provide useful help to customers. The following are some of our original articles, which can be referred toWhat is IGBT heat dissipation? What kind of liquid cooling plate design is optimal, and how the cold plate microchannel of IGBT is designed.
What is a IGBT liquid cold plate?
What is the maximum temperature for IGBT?
All You Need to Know About IGBT Liquid Cooling.
How to design a IGBT Heat sink?