
In Power Electronics, the insulated-gate bipolar transistor (IGBT) is one of the most widely utilized semiconductors. Modern IGBTs are built of Silicon Carbide (SiC) aand Gallium Nitride (GaN) for better production and thermal efficiency.
While IGBTs are helpful for power supply and conversion, they may also create a lot of heat when switched at high frequencies.
The cooling of IGBT devices is a significant concern for electric power engineers.
Development of IGBTs
The IGBT is a stronger switch that operates by controlling the voltage to a semiconductor part to generate an electrical circuit. It was first introduced in the 1980s, and it was enhanced on the metal oxide semiconductor field-effect transistor’s invention (MOSFET).
The IGBT is unusual because it eliminates the thyristor function, resulting in a more efficient device. Inverters, motor drives, and power systems for advanced solar and wind turbines are all made with IGBTs.
Thermal Management of IGBTs
Electric power production, conversion, transmission, and distribution require the use of power electronics equipment. Power technologies are being deployed to increase energy efficiency, dependability, and control. Some experts believe that all electrical power will travel through a power semiconductor device at some point in the future.
IGBTs are high-voltage, high-power gadgets that are becoming increasingly popular. An IGBT (insulated-gate bipolar transistor) is a solid-state switch that enables electricity to flow when it is turned on and shut down.
An IGBT works by delivering a voltage to a semiconductor component, changing its properties and allowing it to block or produce an electrical path.
For moderate frequency (5-50 kHz) and high voltage (200-2,000 V) applications, an IGBT combines an insulated gate input with a bipolar output to produce a dependable power switch.
Large IGBT modules often include multiple devices connected in parallel and can handle hundreds of amperes of current with blocking voltages as high as 6,500 V. Hundreds of kilowatts of power may be controlled by these IGBTs.
IGBTs are used in a wide range of high-power applications, including electric and hybrid vehicles, battery chargers, electric buses, appliance motor drives, switch and power supplies, voltage control converters, motor drive controls, solar and wind power inverters, thermal management, and medical diagnostic devices.
IGBT Cooling Solutions
IGBT thermal control can be aided by a variety of cooling solutions. Each choice comes with its own set of benefits.
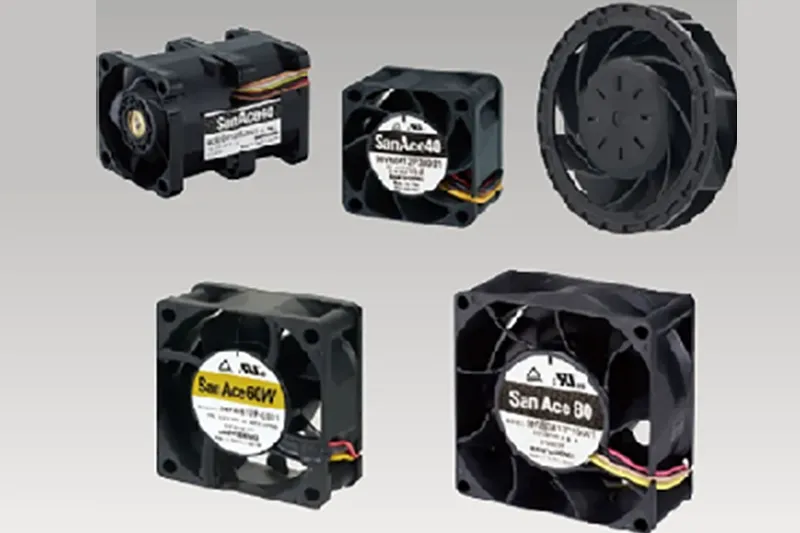
Air Cooling
For low-power systems, air-cooled heat sinks can also be a quick and cost-effective option. To absorb heat and spikes, some industrial designs employ a heat sink with a large mass and thermal capacitance.
Air-cooled heat sinks have a more challenging time handling greater temperatures and thermal spikes in high-power electronic equipment because of the air’s heat-carrying ability and the normal high acoustic operating temperatures as a result, air cooling is only economical for low- and medium-power equipment.
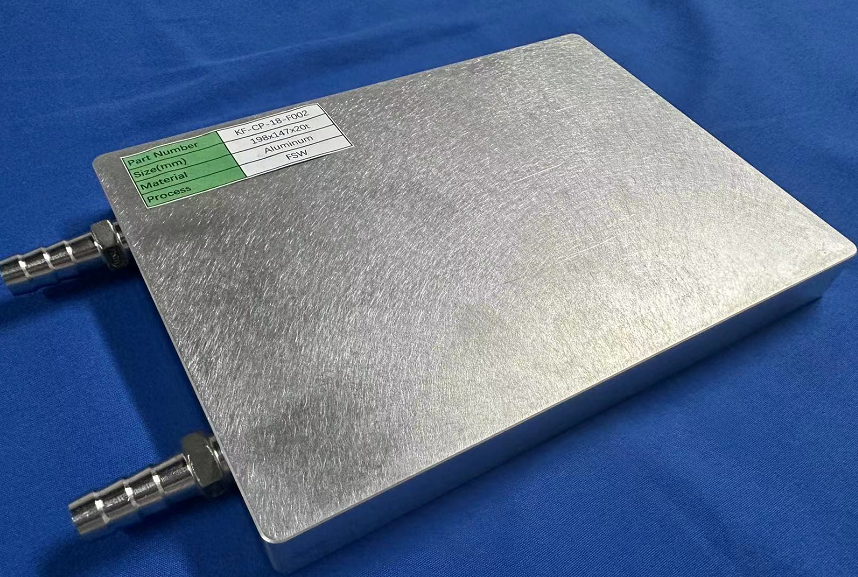
Direct Liquid Cooling
In IGBTs, direct liquid cooling enhances heat transfer characteristics and lowers thermal resistance, decreasing junction temperatures and enhancing power capabilities.
Liquid cooling also enables designers to produce higher power per volume, improving performance and efficiency. Direct liquid cooling has previously been achieved by swaging large copper tube cold plates onto aluminum blocks using thermally conductive epoxy.
Other designs incorporate copper pipes that have been machined to increase efficiency. A pin-fin heat sink is implanted in a DBC substrate, which is subsequently affixed to a fluid reservoir, enabling coolant to circulate over the fins for a cooling effect.

Microchannel Liquid Cooling
An innovative microchannel liquid cooling concept achieves the lowest thermal resistance possible for high-power devices.
When compared to earlier liquid cooling systems, integrated microchannel liquid cooling may reduce the thermal resistance of an IGBT by 10x-100x by reducing the thermal mass of the coolant in mini flow channels.
This considerably improves the thermal transfer rates and functioning temperatures of IGBT system designs. By improving microchannel thermal physics, Kenfatech microchannel cold plates boost performance.
Our microchannel grid designs may be adjusted to match the characteristics of IGBT modules and can provide power electronics with unrivaled and consistent thermal control.
IGBT Application in Power Electronics
IGBTs have gained popularity in power electronics applications during the last few decades. IGBTs provide power to a variety of devices and systems.
Inverters
Because of their excellent gate control and capacity to carry more significant currents, IGBTs are perfect for inverters. Advanced cooling options on IGBT modules enable a more successful transition from DC to AC power.
Converters
Voltage converters are powered by inductively coupled bipolar transistors (IGBTs). In the design of power supply, converters play a crucial role.
Power Supplies
IGBTs may be used with two different power supplies:
● Switch Mode Power Supply (SMPS)
● Uninterruptible Power Supply (UPS)
Switch Mode Power Supply
IGBTs can help with high-current applications, whereas a switching converter is used to convert voltage output in an SMPS.
Uninterrupted Power Supply
An IGBT can assist a UPS in delivering smooth, constant power once an electrical system fails.
Renewable Energy Applications
Renewable energy solutions are being integrated into the strategic plans of a rising number of commercial, industrial, and municipal organizations. Using microchannel technology to optimize IGBT liquid cooling can help customers create more sustainable energy at a reduced cost.
Solar Inverters
Solar inverters take the DC electricity generated by solar panels and convert it to AC power that consumers may use. The IGBT is a crucial component in enabling people to access smarter, cleaner energy, and it must be thermally controlled to function correctly.
Concentrated Photovoltaic Receivers (CPVs)
Hundreds of mirror reflectors are used in concentrating photovoltaics (CPVs) to direct solar energy to a central receiver. The resultant power output generates a heat flow near the sun’s surface!
To ensure constant operation, the CPV receiver, a vital component of the system, must be cooled using highly efficient methods such as microchannel liquid cooling.
Solar Assisted Heat Pumps
To save money on heating, a solar-assisted heat pump combines a regular heat pump with photovoltaic input.
Microchannel cold plates for IGBT power modules can boost energy efficiency while lowering the system’s total cost of ownership.
Conclusion
IGBTs create a lot of heat and can be harmed by too much of it. Because of the huge proportions required to control the massive volumes of heat, using air cooling solutions, such as heat sinks, for high-power dissipation IGBTs can be impracticable.
Liquid cooling has many orders of magnitude greater heat transfer coefficients than convection cooling, allowing for substantially higher power densities and more compact module and inverter solutions. While liquid cooling is sometimes resisted in the power electronics business, it is necessary to fulfill many of today’s IGBT thermal management requirements.
Liquid cooling for internal combustion engines has been utilized in the automobile industry for more than a century, and the idea of utilizing liquid cooling for power electronics in an automotive application is currently regarded as a non-issue. The liquid cooling methods for IGBTs include cold plates, heat pipes, turbulators, and vapor cooling loops.
Kenfatech creates unique IGBT microchannel liquid cooling solutions to assist you in increasing your power electronics system’s power performance, efficiency, safety, and reliability.