Introduction
Battery cooling plates are essential components in the thermal management systems of batteries, particularly in electric vehicles (EVs) and energy storage systems. Adequate cooling is crucial to maintain battery performance, safety, and longevity. As demand for efficient energy solutions grows, understanding the manufacturing process of these plates becomes increasingly essential. This article explores how battery cooling plates are made, their types, materials, manufacturing processes, and critical considerations for buyers when selecting a Battery Cooling Plates manufacturer or supplier.
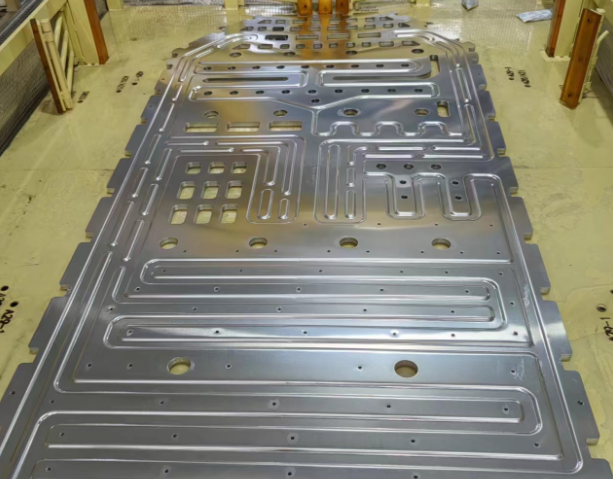
Understanding Battery Cooling Plates
Definition and Function
Battery cooling plates are devices designed to regulate the temperature of battery cells. By managing heat dissipation, these plates ensure the battery operates within optimal temperature ranges, thus preventing overheating and enhancing the battery’s efficiency and lifespan.
Types of Cooling Plates
There are various types of cooling plates used in battery systems, including:
- Liquid-cooled plates: Utilize liquid channels to absorb and transfer heat from the battery cells.
- Air-cooled plates: Airflow dissipates heat and is often employed in less demanding applications.
- Phase-change materials (PCM) cooling plates: Incorporate materials that change phase (e.g., from solid to liquid) to absorb large amounts of heat.
Materials Used in Battery Cooling Plates
Common Materials
The choice of material for battery cooling plates is crucial for their effectiveness. Common materials include:
- Metals (e.g., aluminum, copper): Known for their excellent thermal conductivity.
- Composites: Offer a balance of thermal performance, weight, and durability.
Material Selection Criteria
When selecting materials, several factors must be considered:
Choosing suitable materials ensures that the cooling plates perform effectively and remain reliable throughout their service.
Criteria | Description |
Thermal conductivity | Ability to conduct heat efficiently. |
Weight considerations | Importance of maintaining a lightweight design. |
Corrosion resistance | Durability in various environmental conditions. |
Cost | Balancing material costs with performance benefits. |
Manufacturing Processes
Design and Engineering
The manufacturing process of battery cooling plates begins with precise design and engineering. Using Computer-Aided Design (CAD) software, engineers create detailed models to optimize thermal management. Simulations and testing ensure the designs meet efficiency and performance standards.
Production Techniques
Several production techniques are employed in the manufacture of battery cooling plates, including:
Stamping and Forming
Stamping involves cutting and shaping metal sheets into the desired form. This process is efficient and cost-effective for producing large quantities of cooling plates.
Forming refers to various techniques to shape the metal, such as bending and pressing. These methods help achieve the intricate geometries needed for effective thermal management.
Brazing and Welding
Brazing is a process where two metals are joined using a filler metal with a lower melting point. This technique is crucial for assembling parts of the cooling plate that must maintain a robust and leak-proof bond.
Welding involves fusing materials by melting them at high temperatures. Welding is essential in ensuring the structural integrity of the cooling plates, particularly for liquid-cooled systems.
Extrusion
Extrusion is a process where the material is forced through a die to create long shapes with a consistent cross-section. This method is beneficial for producing cooling plates with complex internal channels that enhance heat dissipation. Extruded cooling plates often feature intricate designs that improve thermal performance.
Bonding and Sealing
Ensuring that liquid-cooled plates are leak-proof is critical. Various bonding and sealing techniques, such as adhesives and gaskets, are employed to prevent leaks and ensure the longevity of the cooling plates. Quality control measures are rigorously applied to detect and address any potential issues.
Quality Assurance and Testing
Thermal Performance Testing
Testing the thermal performance of battery cooling plates involves measuring their ability to conduct and dissipate heat. Infrared thermography and thermal cycling tests ensure the cooling plates can maintain efficient heat transfer under various conditions.
Durability Testing
Durability tests assess the mechanical strength and corrosion resistance of the cooling plates. These tests include stress tests that simulate real-world operating conditions to ensure the plates can withstand physical and chemical stresses over their lifespan.
Leak Testing
Leak testing is essential for liquid-cooled plates to maintain system integrity. Procedures like pressure and vacuum testing ensure that there are no leaks in the cooling channels. Detecting and fixing leaks is crucial for the safe and efficient operation of the battery cooling system.
Considerations for Buyers
When selecting a Battery Cooling Plates manufacturer or supplier, several key factors should be considered to ensure optimal performance and reliability of the cooling plates.
Compatibility with Battery Systems
Ensuring that the cooling plate matches the battery design is essential. Compatibility involves fitting the cooling plate precisely to the battery cells and the overall system architecture. Buyers should verify that the cooling plate specifications align with their battery system’s requirements.
Performance Requirements
Evaluating the cooling efficiency based on your system’s needs is critical. This includes assessing the cooling plate’s ability to manage thermal loads during peak and normal operating conditions. Performance metrics such as thermal conductivity and heat dissipation should be closely examined.
Supplier Reliability
Choosing a reputable Battery Cooling Plates supplier is crucial for obtaining high-quality products. Factors to consider include:
- Track record: Look for suppliers with a history of reliability and quality.
- Certifications: Ensure the supplier meets industry standards and certifications.
- Customer support: Strong after-sales support and warranties can indicate a trustworthy supplier.
Cost vs. Performance
Balancing initial costs with long-term performance benefits is essential for making a sound investment. While high-quality cooling plates might come at a premium, their efficiency and durability can result in lower maintenance costs and longer service life, offering a better return on investment (ROI).
Consideration | Importance |
Initial cost | Budget constraints and upfront investment. |
Long-term performance | Efficiency, durability, and maintenance costs. |
ROI considerations | Balancing cost with benefits over time. |
Conclusion
When selecting battery cooling plates, it is vital to consider factors such as compatibility, performance requirements, supplier reliability, and cost-effectiveness. Working with a knowledgeable Battery Cooling Plates manufacturer or supplier can help you make informed decisions that enhance the performance and longevity of your battery systems.
For specific needs, consulting with experts or manufacturers is recommended to ensure that the selected cooling plates meet all operational and performance criteria. By understanding the materials, manufacturing processes, and quality assurance methods, buyers can make educated choices and invest in high-quality cooling solutions.